Signs You Need Professional Packaging Machine Repair Right Away
Signs You Need Professional Packaging Machine Repair Right Away
Blog Article
Quick and Reliable Packaging Maker Repair Service Solutions to Lessen Downtime
In the competitive landscape of manufacturing, the efficiency of packaging operations hinges on the reliability of equipment. Quick and dependable repair solutions are vital in mitigating downtime, which can lead to substantial economic losses and functional troubles.
Importance of Timely Repair Works
Timely repair work of product packaging equipments are important for preserving operational efficiency and lessening downtime. In the hectic environment of production and packaging, also minor malfunctions can result in substantial delays and productivity losses. Resolving problems without delay makes sure that equipments operate at their optimum ability, consequently guarding the flow of procedures.
Additionally, normal and prompt maintenance can prevent the escalation of small troubles right into major breakdowns, which typically sustain higher repair service costs and longer downtimes. A proactive method to equipment repair service not just protects the honesty of the devices but also boosts the overall reliability of the assembly line.
In addition, prompt repair services contribute to the durability of product packaging machinery. Machines that are serviced immediately are much less likely to struggle with too much deterioration, allowing organizations to maximize their investments. This is particularly essential in industries where high-speed packaging is vital, as the requirement for consistent performance is critical.
Advantages of Reliable Company
Reliable solution suppliers play a pivotal role in guaranteeing the smooth procedure of product packaging equipments. Their expertise not only boosts the efficiency of repair services but likewise contributes substantially to the long life of equipment.

Furthermore, a trustworthy solution company uses extensive assistance, consisting of training and support for team on machine procedure and upkeep ideal practices. This not only equips employees however additionally grows a culture of security and efficiency within the company. Overall, the advantages of involving reliable solution companies extend past immediate repair services, positively influencing the whole functional operations of packaging procedures.
Typical Packaging Equipment Problems
In the realm of product packaging operations, numerous issues can compromise the performance and capability of makers (packaging machine repair). One more common issue is imbalance, which can cause jams and uneven packaging, impacting item high quality and throughput.
Electrical troubles can also interfere with packaging operations. Defective wiring read this article or malfunctioning sensing units may lead to erratic device behavior, creating delays and increased operational prices. In addition, software application glitches can impede the maker's programming, leading to operational inefficiencies.
Inconsistent product circulation is another vital problem. This can occur from variations in product weight, size, or shape, which may impact the maker's capability to handle products precisely. Ultimately, insufficient training of operators can aggravate these troubles, as untrained employees might not identify very early indications of breakdown or may abuse the tools.
Attending to these common packaging maker problems quickly is vital to keeping productivity and guaranteeing a smooth procedure. Normal assessments and aggressive upkeep can substantially mitigate these problems, promoting a dependable product packaging environment.
Tips for Lessening Downtime
To decrease downtime in packaging operations, carrying out an aggressive upkeep approach is vital. On a regular basis scheduled maintenance checks can identify potential problems prior to they intensify, guaranteeing devices operate efficiently. Developing a regimen that consists of lubrication, calibration, and evaluation of vital components can significantly reduce the regularity of unexpected break downs.
Educating team to run equipment appropriately and identify very early indication of breakdown can additionally play a crucial role. Encouraging operators with the understanding to carry out basic troubleshooting can avoid small concerns from creating major delays. Furthermore, preserving a well-organized stock of vital spare components can expedite fixings, as awaiting components can bring about prolonged downtime.
Additionally, recording maker performance and maintenance tasks can aid identify patterns check that and frequent issues, permitting targeted interventions. Incorporating advanced surveillance innovations can supply real-time data, enabling predictive upkeep and minimizing the risk of unexpected failings.
Lastly, promoting open communication in between drivers and upkeep teams makes certain that any type of irregularities are quickly reported and dealt with. By taking these proactive measures, services can boost functional effectiveness and considerably lower downtime in product packaging procedures.
Selecting the Right Fixing Service
Picking the proper repair solution for product packaging machines is a crucial decision that can dramatically impact operational effectiveness. Begin by assessing the service provider's experience with your certain type of product web link packaging devices.
Following, take into consideration the provider's track record. Looking for comments from other services within your sector can give understandings into integrity and high quality. Accreditations and collaborations with recognized tools producers can additionally show a dedication to excellence.
Additionally, assess their feedback time and schedule. A provider that can provide timely support decreases downtime and keeps production circulation stable. It's likewise vital to ask concerning service warranty and solution guarantees, which can reflect the self-confidence the service provider has in their work.
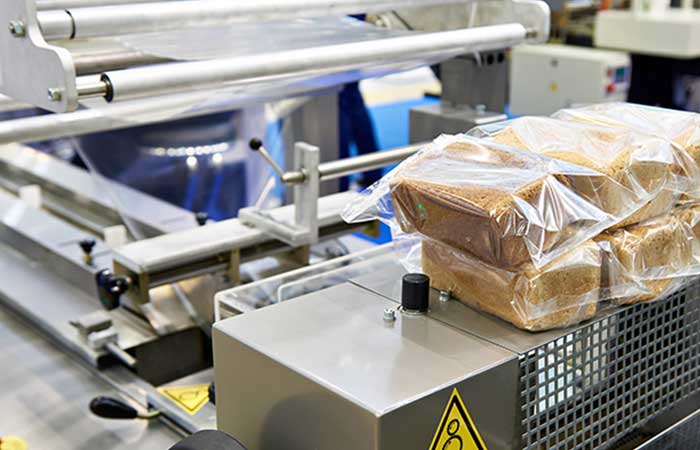
Conclusion
To conclude, the significance of fast and dependable packaging maker repair services can not be overstated, as they play an essential duty in decreasing downtime and ensuring functional efficiency. By focusing on prompt repairs and choosing reputable company, services can successfully address typical concerns and maintain performance. Implementing aggressive maintenance techniques and investing in team training further improves the long life of packaging equipment. Ultimately, a strategic approach to repair services fosters an extra resistant manufacturing environment.
Timely fixings of product packaging equipments are essential for keeping operational efficiency and decreasing downtime.Additionally, prompt fixings add to the long life of packaging equipment. In general, the advantages of involving trustworthy solution suppliers prolong beyond instant fixings, positively impacting the whole operational workflow of packaging processes.
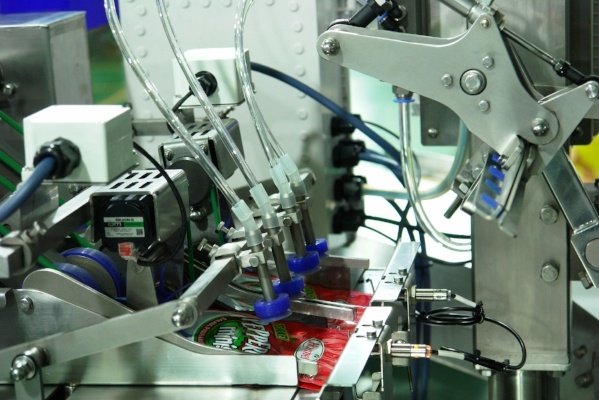
Report this page